網站內容顯示

Advantest Group Quality Policy
“Customer Satisfaction” is the fundamental basis of all our activity.
We are committed to providing customer-satisfying products in a timely manner,
by activating quality implementation from early in the design stage,
and increasing the total efficiency of our overall sales and manufacturing process.
Quality Management System
In keeping with our product quality plan, which calls for improvement in customer satisfaction, we have designed our quality management system to comply with the international quality assurance standard ISO9001 throughout the Company.
We have established an organization to promote the system within the company-wide framework, led by the Quality Assurance Manager under the supervision of executive management, which maintains and improves quality systems, with the goal of raising customer satisfaction. We have also constructed our own internal audit framework, and we maintain and improve our systems through regular internal audits.
SQE Activities
We are committed to the notion that individual components underpin overall product quality, and therefore the quality of each and every component has to be exceptional. Premised on that assertion, the Advantest Group engages in SQE (Supplier Quality Engineering) initiatives beginning at the component adoption phase, drawing on the support of our supplier network. SQE initiatives are undertaken with the aim of enlisting a team of experts to bring about improvements to component quality. Accordingly, it is critical that we engage in practices to ensure component quality, particularly given that the number of parts used in our products is roughly equivalent to the 200,000 to 3,000,000 parts that make up an aircraft.
Our SQE initiatives involve the following three practices.
- Careful selection of components: When given the choice of multiple components with similar performance specifications, we select the best item through a process involving in-house quality analysis and evaluation.
- Quality improvement through PDCA: We apply PDCA-cycle practices from the component design phase to manufacturing to achieve improvements prior to high-volume production and thereafter.
- Ensuring that tolerances are maintained in component design: We aim for component design benchmarks determined on the basis of tolerances rather than standard specifications.
In this way, by running SQE activities from the product development stage, we can reduce problems with components in the manufacturing process and the risk of component problems reaching the marketplace, which contributes to greatly reducing the risk of losses. The results of this approach can be seen in the smooth running of our end users’ processes and in the increased security that our clients enjoy in using our products.
Also, by decreasing the incidence of rejected parts we decrease the need for their exchange and disposal, and so contribute to reducing the environmental impact.
Securing Product Safety and Quality
Aiming to meet the high product safety standards increasingly seen as important by modern society, we adopted the Advantest Product Safety Charter in May 1995.
To achieve the above, we formulated our Product Safety Promotion Regulations and established a companywide committee as an organization to promote advances in product safety. From May 1995 to the present, this committee has been continually active in product safety improvements.
In fiscal 2015, we commissioned specialist outside bodies to undertake inspections of the safety and durability of 13 Advantest’s major products. The results indicated that there was no need for further revision of improvement of Advantest’s safety specifications.
It should be noted that, in fiscal 2015, there were no violations of the standards specified in Advantest’s Product Safety Promotion Regulations.
Initiatives Aimed at Improving Software Quality
Advantest continues to implement initiatives aimed at improving software quality. Software for test systems, handlers and other such systems shipped by Advantest first goes through a process that involves quality verification by the Quality Assurance Division. The specification sheet, a parallel product of development, is examined by the Quality Assurance Division in real time and feedback is given, which helps to ensure quality at upstream stages of development. The examination is implemented by the time development is complete, and after fulfillment of quality standards is confirmed, products are shipped.
Beginning in 2012, process improvement activity using the “Toyota development process”*1 has been implemented with the cooperation of the R&D Division. This activity improves the level of the design review process, and high-quality design enables high-quality and high-throughput product development. These initiatives help to bring about the timely delivery of even better products.
*1 Source: The Toyota Product Development System, James M. Morgan, Jeffrey K. Liker, 2006.
Availability
Advantest is committed to helping its customers achieve higher levels of productivity by offering them products that guarantee high availability — meaning that they are unlikely to malfunction, and will recover immediately should failure occur. More specifically, availability refers to the ratio of time that a system is operational over a given time, and as such constitutes one of the benchmarks of product integrity. The Advantest Group delivers high availability by working hard to improve MTBF*1 so that systems will operate without malfunction over longer duration of use, while also reducing MTTR*2 so that systems will be more readily serviceable when malfunction does occur.
*1 MTBF: mean time between failure
*2 MTTR: mean time to repair
Design Review System Aimed at Improving Quality
Persistently stringent customer demands for functionality, performance and quality create demand for Advantest products equipped with increasingly large-scale and progressively more complex circuitry. Meanwhile, we are also responding to demands for shorter development lead times, a challenge we feel is best addressed by instilling quality at the upstream design phase so that we can detect potential issues early on. Accordingly, we introduced a new design review system in 2008 as a framework for achieving these goals.
- Our design review system was amended to ensure that the project leader establishes a design review plan when product development begins, and so that reviews are conducted regularly.
- We changed the system so that the relevant staff and the project leader, as well as the quality assurance division, carry out monitoring to prevent follow-up omissions, by enabling visual identification of issues raised.
- We also adopted the Design Review Meister System, which involves forming groups of in-house experts for each technical area to participate in the related design reviews. This system increases the rate of problem detection in design reviews, encourages the succession of technologies, and facilitates in-house education.
Many positive results have been achieved through these activities. For instance, the rate of defect detection during the design phase has recently improved, leading to a decrease in setbacks and fewer defects finding their way into the post process, thereby minimizing development delays. The new design review system has resulted in improvements in design quality and a reduction in development lead times. However, it has also revealed some cases in which problems that should have been detected by the designer ultimately found their way into the design review or the post process.
Advantest regularly collects analysis and feedback on issues that have gone undetected and makes improvements to the review framework as necessary. Moreover, going forward we will implement further improvements to the design process involving thorough checking prior to design reviews to achieve better design quality.
Basic Policy for Improving Customer Satisfaction
Customer satisfaction is the most fundamental of principles underpinning Advantest’s business. Our product quality policy, which is shared throughout the Group — “Elaborate for quality from the design stage, promote to optimize the whole process of manufacturing, and offer the timely and high-quality products our customers expect” — characterizes our portfolio of products that offer not only superior performance, but also superior environmental friendliness and safety. We are committed to keeping our customers satisfied at every stage, from design and manufacturing to sales and service, via guaranteed quality, top-notch service, and support on a global scale.
Sales and Marketing Practices that Support Customer Satisfaction Gains
The mobile device market, consisting mainly of tablets and smartphones, has been the leading source of demand for semiconductors in recent years, and demand shifts in this market are growing larger. It is imperative for Advantest to respond to these shifts by strengthening its product supply system through parts procurement readiness, shortening of manufacturing processes, and reduction of production costs. In line with this, we implemented the integration of our factory in Gunma in September 2014.
Previously we performed manufacturing of semiconductor test systems and installing of boards used for them in separate factories, but by integrating these processes into one factory we were able to streamline the overall production process. Through this we have been able to establish a manufacturing set-up able to respond to our customers’ steadily changing business environments.
At the same time, in the case of device interfaces, which require customization for customer products, we are working to establish production bases close to customers in China, Korea and South East Asia, in order to be able to respond directly to customer needs and achieve fast delivery times.
We are aiming to further improve customer satisfaction through these measures.
Sales and Marketing Activities to Improve Customer Satisfaction
The semiconductor industry, which Advantest supports through its products, is an industry characterized by intense competition to develop next-generation technologies. Besides providing our customers with test solutions, Advantest also holds the annual VOICE Advantest Developer Conference, at which we share the latest technology and product information with our partner companies. In fiscal 2015, for the first time, the VOICE Advantest Developer Conference was held on two continents in the same year, being held in Silicon Valley in the U.S. in May 2015 and also in Shanghai, China, with a record 400-plus people participating. Besides this expansion in the geographical scope of the Conference, another thing that made this year’s Conference special was that 41% of the technical papers submitted for the Conference were from authors who had not participated before, while the number of countries represented rose to a record 14; overall, this year saw a big step forward in terms of both quality and quantity. This year, besides presenting Advantest’s new products and technologies, the Conference also showcased the solutions of 13 strategic sponsors, and benefited from support from four prestigious industry bodies – SEMI, the Global Semiconductor Alliance (GSA), VLSI Research, and IC Insights – providing opportunities for strengthening linkages within the industry. The 2016 VOICE Advantest Developer Conference was the 10th Conference, making this a very special occasion, and encouraging us to do our best to provide an even richer array of content than usual.
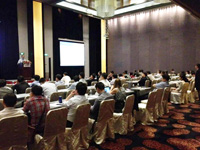
Scene of presentation
Advantest has also continued to hold technical seminars at locations throughout the world, with the aim of presenting the latest information about our products and enhancing communication with customers. In 2015, technical seminars were held in June 2015 in Tel Aviv, Israel, in October 2015 in Seoul, South Korea, and in November 2015 in Shanghai and Beijing, China. We were delighted to see so many Advantest customers attending these events.
In the future, Advantest will continue to hold events worldwide aimed at helping us to better understand customer needs and strengthen communication with customers, which in turn can help us to enhance our customer service provision.
Promoting Customer Support
The Advantest Group has established its basic policy for customer support with the aim of realizing the globally-oriented restructuring of the Group’s service businesses.
Our basic policy is outlined as follows.
< Basic policy for customer support >
- We will propose total solutions in the form of support packages designed to deliver maximum efficiency to our customers in their device measurement operations.
- We will propose unified service support matching the customer’s business model from development to the mass production environment.
- We will respond to customer demands by proposing service support packages that encompass total solutions.
- We will always take the customer’s point of view and draw on our global organization in offering solutions.
- Our premium services and customer support will not only be efficient, but will also take the environment and safety into consideration.
- We will offer high-value-added professional services.
- We will strive to maintain our zero-accident record by thoroughly observing safety standards in field service provision and elsewhere.
Better Customer Support with a Global Focus
Advantest is building a global support framework capable of responding effectively to service support requests and other inquiries from customers. While responding to everyday service support requests through contact centers in each country, as well as by telephone and e-mail, we are also implementing primary support consisting of technical service and onsite repairs by field engineers.
We station expert support teams in product development bases to carry out secondary support, allowing us to respond appropriately to the content and difficulty of service requests.
We have developed a global supply-chain network covering customer operations ranging from their development bases to mass production facilities. Moreover, we also operate a supply-chain control mechanism through which replacement equipment and parts at service centers in each country are monitored to determine inventory needs at respective locations worldwide.
We continue to run an engineer exchange program between overseas subsidiaries and our secondary support division, which helps engineers to improve their professional skills and raises the quality of our support. This two- to three-year program aims to sharpen engineers’ technical skills, develop cross-cultural competencies, and raise foreign language and communication proficiencies. In the mass production facilities of customers, we offer on-request expert consulting and solutions regarding productivity issues. Also, we offer device measurement training to our customers, and provide professional advice in that regard.
Global Support Center System
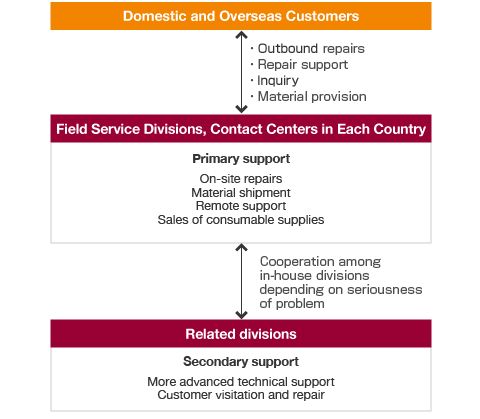
Recipient of the “10 BEST” Customer Satisfaction Award for the 28th Consecutive Year, on the Basis of the VLSI Research Survey
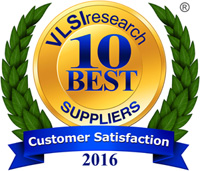
VLSI Research: 10 BEST
Advantest aims for a clear grasp of customer needs and strives to provide customers with high-performance, premium-quality total test solutions in a timely manner.
At Advantest, we gain a better understanding of our customers’ needs through information that we acquire from our daily business activities, and also through yearly participation in the customer satisfaction survey conducted by VLSI Research, a company renowned for its semiconductor market research. Based on this year's survey, we received the “10 BEST” award granted to the top-ten ranking companies for the 28th year in a row.