Materiality for the Advantest Group
Our Approach to Materiality
At Advantest, we believe that it is vitally important to first identify the impacts that our company’s operations have on society and the problems that society expects us to help solve, as a basis for clarifying the key issues that we need to address in our CSR activities, so that we can then go on to implement effective management based on specific key performance indicators (KPIs).
To this end, in FY2015 we used a three-step process with reference to the Global Reporting Initiative (GRI) G4 Sustainability Reporting Guidelines, to identify what constitutes materiality for the Advantest Group.
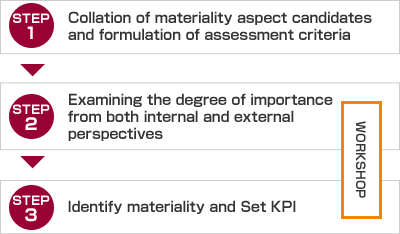
The Process of Identifying Materiality
Step 1: Collation of materiality aspect candidates and formulation of assessment criteria
A total of 50 materiality aspect candidates were identified on the basis of the 46 aspects listed in the Global Reporting Initiative (GRI) G4 Sustainability Reporting Guidelines, the requirements of the EICC® *, industry standards such as SASB*, and information obtained from CSR surveys submitted to customers.
Assessment criteria were then formulated so as to be able to rank the materiality aspect candidates in priority order, taking into account the need to maintain consistency with respect to boundaries and business risk.
* EICC®: Electronic Industry Citizenship Coalition / Electronic Industry Code of Conduct
* SASB: Sustainability Accounting Standards Board (U.S.A.)
Step 2: Examining the degree of importance from both internal and external perspectives
A Materiality Identification Project Team was established (with Team members that included CSR Working Group members, representatives of relevant departments and responsible directors), and three Workshops were held. Materiality was examined in terms of both the level of importance as viewed by stakeholders, and the degree of importance to the Advantest Group.
Step 3: Identify materiality and set KPI
The identified materiality items were submitted to the Managing Executive Officers Committee for approval.
Following the approval of the materiality items by the Managing Executive Officers Committee, the Materiality Identification Project Team discussed the key performance indicators (KPIs). KPIs were set with 1 – 2 indicators per materiality aspect.
Identified Materiality Aspects and Corresponding KPIs Aspects
Category | Identified materiality aspect | KPI | Measures implemented |
---|---|---|---|
Economy | Economic performance | Sales and operating income margin | Economic Impact |
Intellectual property rights protection | Percentage of employees who have undergone e-learning training relating to intellectual property rights protection | Intellectual Property Protection | |
Environment | Energy | Rate of improvement in per-unit energy consumption | Global Warming Prevention |
Emissions into the atmosphere | Greenhouse gas emissions (Scope 1 and Scope 2) | Global Warming Prevention | |
Discharged water and waste | Waste recycling rate | Recycling Resources | |
Hazardous substances | Percentage of suppliers covered by hazardous substance surveys | Environmental Risk and Chemical Substance Management | |
Products and services | Percentage of products meeting own green products criteria | Green Products | |
Compliance | Number of environmental non-compliance | Environmental Communication / Environmental Contribution Activities | |
Supplier environmental assessment | Percentage of new suppliers that were screened using environmental impact criteria | Procurement Practices | |
Society | Conflict minerals | Continuing efforts to use materials where the risk that said minerals have been produced using conflict minerals is low, by asking business partners to ensure transparency in regard to the sources of materials and components, etc., and by working together with industry organizations and business partners to investigate information relating to conflict minerals (i.e. mineral processing firm information). | Procurement Practices |
Employment | Percentage of employees returning to work after taking childbirth and/or childcare leave | Employment and Diversity | |
Occupational health and safety | Occupational accident rate in Japan | Occupational Health and Safety | |
Training and education | Average number of hours of training per employee per year | Human Resources Development, Fair Evaluation and Treatment | |
Diversity and equal opportunity | Female employees as percentage of total workforce | Employment and Diversity | |
Supplier labor practices assessment | Percentage of new suppliers that were screened using labor practices criteria | Procurement Practices | |
Non-discrimination | Number of complaints submitted to the helpline that are properly resolved | Compliance | |
Supplier human rights assessment | Percentage of new suppliers that were screened using human rights criteria | Procurement Practices | |
Anti-corruption | Number of confirmed incidents of improper behavior | Compliance | |
Compliance with anti-monopoly legislation | Number of incidents relating to relevant legislation | Compliance | |
Compliance | Number of non-compliance instances relating to social issues | Compliance | |
Supplier assessment for impact on society | Percentage of new suppliers that were screened using criteria for impacts on society | Procurement Practices | |
Customer health and safety | Number of non-compliance of own safety standards | Product Liability | |
Customer privacy | Number of complaints relating to information security | Risk Management | |
Compliance | Number of non-compliance relating to products/services | Product Liability |
A Message from Advantest’s Director of CSR
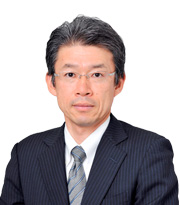
All Advantest’s stakeholders expect us to reconcile the requirements of a sustainable society with the imperatives of our own corporate development. Based on a long-term perspective, we consider our business and CSR activities to be the natural starting point for us to contribute to the various challenges of modern society through our measurement technologies. While bearing our origins in mind, we will fulfill our dual responsibility to improve corporate value by generating profit, and contribute to the development of a sustainable society, throughout all our corporate activities, including our supply chain.
In fiscal 2015, we launched a project to formulate materialities, staffed by our in-house CSR working group, the managers of relevant departments, and executive officers with related responsibilities. The project discussed which topics to emphasize and identified 24 materialities. This initiative also prompted a review of our business development process from the perspectives of supply chain complexity and delegation of responsibilities.
In FY2016, we established KPIs (Key Performance Indicators) for each materiality identified, and have started activities targeted for completion in FY2018. Regarding the reduction of overtime hours, we have been able to hold overtime to a slight increase compared with the previous fiscal year, despite rapid growth in our business. In green products, we have delivered significant reductions in power consumption and footprint in our new products. Moreover, as part of our commitment to environmental management, we have promoted environmental measures in various areas, such as purchasing a 100% green electricity supply for offices in the United States.
In FY2017, we will further promote activities designed to achieve our objectives, and will enhance our worldwide CSR efforts via activities in the 16 countries in North America, Europe, Asia and other regions where we have a business presence.
Koichi Tsukui (Director and Managing Executive Officer)