웹 내용 전시

Power saving initiatives at Advantest Group
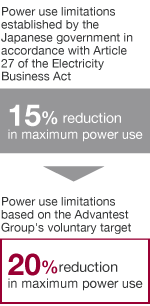
The Great East Japan Earthquake that occurred on March 11, 2011 caused catastrophic damage to people in the local community and buildings, especially in the Tohoku region. The Fukushima Daiichi Nuclear Power Station and other power supply facilities were severely affected by the earthquake, leading to a serious power shortage in the Kanto and Tohoku regions. Power shortages can cause significant impact on the lives of people in the local community as well as corporate activities. This can result in an impediment to economic and industrial development, and ultimately hinder the provision of aid to the affected areas.
Up until now, the Advantest Group has formulated Environmental Action Plans as it has worked towards preventing global warming. However, in consideration of the even harsher situation the Group faces, it has been decided that efficient activities that produce high results are necessary. Mainly under the initiative of the Energy Saving Committee and the Global Warming Prevention Committee, studies were conducted on energy saving initiatives that will also lead to productivity improvements and activities at business sites and offices, such as effective energy saving measures for the summer when the amount of energy consumed tends to increase. The decision was then made to deploy these initiatives across the entire Group.
- Initiatives at Advantest Component, Inc.
- Initiatives at the Saitama R&D Center, Gunma R&D Center, Gunma Factory, Gunma Factory 2, and Advantest Laboratories / Sendai Factory
- Initiatives at other offices
Results of initiatives
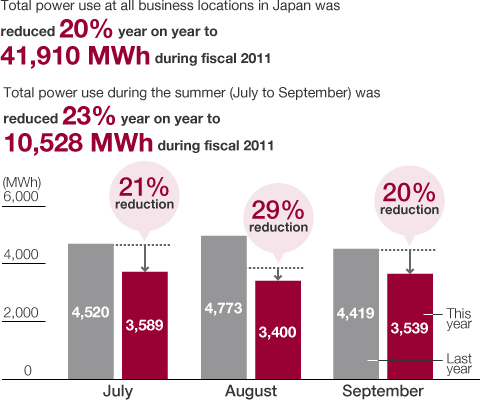
Initiatives at Advantest Component, Inc.
Clean room air conditioning control framework
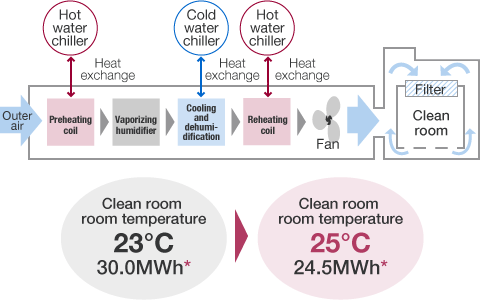
∗ Daily total for Building 3 and Building A during peak demand
Comparison of energy used at Advantest Laboratories / Sendai Factory from July 1 to September 2 (64 days)
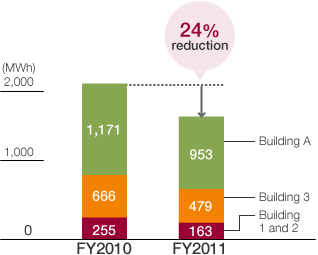
Following the occurrence of the Great East Japan Earthquake, Advantest Component Inc., worked to restore its research and production functions after ensuring the safety of employees and their families. It was at that time that Article 27 of the Electricity Business Act came into effect due to the great damage caused to power companies. In response, the Advantest Group set a voluntary target of a 20% reduction in summer power use, and Advantest Laboratories / Sendai Factory also participated in the Group-wide power saving measures that ensued.
Activities focused on reducing the amount of power used by the clean room air conditioning system, which accounts for 70% of all power used. At the same time, initiatives including lighting reductions and thorough cutbacks in air conditioning in general office rooms were conducted.
It was determined through analysis of power data that it would be possible to achieve the target by raising the clean room temperature 2°C from 23°C to 25°C, but this would have a very significant impact on manufacturing that requires accuracy at the one-hundred-thousandth of a millimeter level.
In particular, processes for which it would be difficult to adjust manufacturing conditions were concluded in advance through production adjustments. In addition, for the hundreds of other processes, adjustments to manufacturing conditions were made as required, the clean room temperature was set to 25°C, and manufacturing work was carried out.
As a result of these energy saving activities, a 20% reduction in peak daytime power use was achieved over a 64-day period at Advantest Laboratories / Sendai Factory from July 1 to September 2 2011, representing a 497 MWh(24%) reduction in power use year on year.
Although the future of the power supply provided by power companies still remains uncertain, we will gather information from various sources as we continue our energy saving measures during the summer of 2012 as well as the long-term future.
Initiatives at the Saitama R&D Center, Gunma R&D Center, Gunma Factory, Gunma Factory 2, and Advantest Laboratories / Sendai Factory
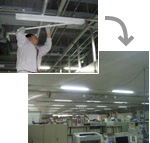
Fluorescent light tube
reductions
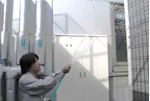
Sprinkling water on walls
At five of the Advantest Group's business locations, the Saitama R&D Center, Gunma R&D Center, Gunma Factory, Gunma Factory 2, and Advantest Laboratories / Sendai Factory, the Group set the target of a 20% reduction in maximum power use, going beyond the Japanese government's target of a 15% reduction. Based on this target, the Group implemented summer power saving measures.
It is essential for companies to secure the quantity of power required for their business activities. Limiting the amount of power that can be used can result in reductions in work efficiency and delays in lead time. If corporate earnings are reduced as a result, it could indirectly impede the recovery of the areas that were affected by the earthquake. In response to these risks, private power generators were installed at three business locations (Gunma R&D Center, Gunma Factory, and Gunma Factory 2) with high contract power. By securing our power sources, we were able to curb the quantity of power that was purchased from power companies. While giving sufficient consideration to our business activities, various other energy saving measures were conducted as well, including a reduction in fluorescent lighting and cutbacks in illumination intensity after confirming the levels of lighting required for safe business operations, and the implementation of optimal operations based on tests that were conducted on the operation time of facilities. Through these measures, a 35% year on year reduction in maximum power use was achieved from July to September 2011 at the five business locations the regulations apply to.
List of energy saving measures at business sites
- Fluorescent lighting reductions and lowering illumination intensity
- Adoption of LED lights
- Sprinkling water on roofs and walls
- Switching over to higher efficiency equipment (such as servers, kitchen refrigerators, and air conditioners)
- Covering windows with shade film
- Shifting from electricity to heavy oil and gas as the primary source of power for air conditioners
- Storing power for nighttime operations
- Partial suspension of vending machines and electric water heaters
Initiatives at other offices
The Advantest Group established the Energy Saving Working Group in June 2011 as an organization to plan and implement energy saving initiatives to be taken on by our offices. The activities decided on by this Group are communicated to all employees through our Internet-based news system and corporate magazine. The initiatives that were adopted for offices include the thorough implementation of the "Cool Biz" campaign and shutting off lights, optimization of room temperatures, and having employees turn the power off monitors when they leave their seats. Although these initiatives may seem like little things in and of themselves, in aggregate they can be expected to produce big results.
In addition, to improve the awareness of each and every one of our employees towards energy saving, a monitor system has been installed that makes it possible to view the amount of power used at business locations over the intranet. This system makes it possible to view the amount of power used, contract power, maximum power, and target power for business locations that are subject to the power use restrictions.
The power monitor
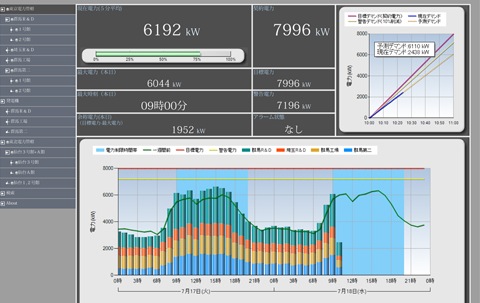
Moreover, if over 80% of the preset target power is used, the system makes an announcement within the building, automatically cuts off some lighting on office floors and laboratories, and reduces the air conditioning.
As a result of these efforts, we managed at all times to clear the power targets that were set for the summer of fiscal 2011.
List of energy saving measures at offices
- Implementation of the "Cool Biz" campaign
- Personnel limited to owning one personal PC and monitor
- Thorough enforcement of PC energy-saving settings
- Thorough enforcement of turning off lights during lunch breaks and when leaving the office
- Turning the power off of office equipment when not in use
- Setting the air conditioning temperature at 28°C for office floors, meeting rooms, and hallways as a general rule
- Rotating operations involving summer vacation shifts by business site