Quality Management

Quality management system
In keeping with a strict company-wide mandate of continuously improving customer satisfaction, our quality management system has been designed to comply with the international quality assurance standard ISO9001.
Lead by the Quality Assurance Manager under the supervision of executive management, an organizational framework has been established that promotes a culture of quality management throughout the company. In addition, an independent internal audit framework regularly conducts internal audits, helping to continually maintain and improve quality systems.
Fiscal 2012 saw the expansion of Group companies and a number of significant changes, including revisions to our quality manuals and the upgrading of internal audits.
ISO9001 certification
Applied Standard | ISO9001:2008 |
---|---|
Certificate Registration No. | 12 100 15196 TMS |
Applied Scope | Design, Development, Manufacture, Sales, Installation, Calibration Service and Support of IC Test Systems, Electron Beam Lithography Systems, Electron Beam Inspection Systems, Optical Sensing Products, Terahertz-wave Application Measurement Systems and Electronic Measuring Instruments |
Certification Body | TÜV SÜD Management Service GmbH |
First Certified | June, 1993 |
Facilities Covered | Advantest Corporation, Japan Engineering Co., Ltd., Advantest Kyushu Systems Co., Ltd., Advantest Component, Inc. |
Design review system aimed at improving quality
Functionality, performance and quality are hallmarks of Advantest products and are expected by our customers. To continually meet these high standards, Advantest must anticipate the challenges of each new generation of technology, such as today’s complex, SOC chips. . Advantest must also meet calls for reduction in development lead times. In order to respond to these demands, we believe instill quality at the upstream design phase which enables us to promptly detect potential issues. A new design review system was introduced in fiscal 2008 as a framework for achieving these goals.
Although Advantest had conducted design reviews previously, there were no rules stipulating that a design review plan had to be established in advance and the frequency and content of reviews varied considerably depending on the division. Furthermore, setbacks occurred as a result of less than timely reviews. The following framework has been adopted for the new design review system to address these problems.
- The system was amended to ensure that the project leader establishes a design review plan when product development begins, and that reviews are conducted regularly.
- The system was changed so that the responsible staff and project leader, as well as the quality assurance division, carry out monitoring to prevent follow-up omissions, by enabling visual identification of issues raised.
- The Design Review Meister System was adopted, which involves forming groups of in-house experts for each technical area to participate in the related design reviews. This system increases the problem detection rate in design reviews, encourages the succession of technologies, and promotes in-house education.
Design Review Meister System
Development process and design quality assurance system
Design Review Meister System organizational chart
Many positive results have been achieved through these activities. Recently the rate of defect detection during the design phase has improved, leading to a decrease in setbacks and the number of defects that find their way into later processes, resulting in minimizing of development delays. The new design review system has resulted in improvements in design quality and a reduction in development lead times. However, it has also revealed many cases in which problems that should have been detected by the designer were allowed to find their way into the design review or later processes.
Although Advantest regularly collects analysis and feedback on issues that go undetected and makes improvements to the review framework in response, in the future we will make further improvements to the design process through thorough advanced confirmation before design reviews to achieve higher design quality.
Reliability design utilizing a framework to assess all failure data
To ensure reliability throughout the entire product life cycle, at Advantest we try to eliminate all elements that could lead to failures and defects from the product design phase. As a foundation for achieving this, we have established an integrated quality management system that aggregates quality-related information in a database containing information such as the number of market defects and shipment parameters for all parts used in products since 2005. This data is then used to estimate the reliability of new products, and if the target reliability is not achieved, the design of the applicable parts and devices is reviewed.
However, in addition to parts that resulted in market defects, this database also includes parts that were used as replacements, making it necessary for staff members to isolate data on defective parts from other data. Because this situation affects the homogenization of data, the accuracy of data has been improved through the addition of a function that automatically filters data on defective parts so that highly reliable parts can be efficiently selected. This framework has facilitated the achievement of targets by making it possible to focus on activities aimed at reliability improvements.
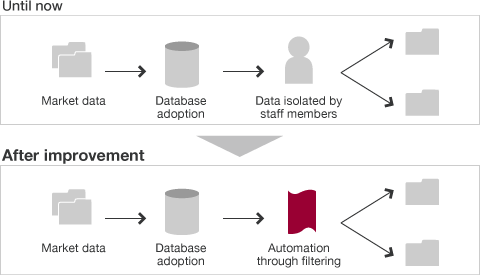
Initiatives aimed at improving software quality
Before Advantest ships software that controls devices such as testers and handlers, quality is confirmed by the quality assurance division after development has been completed by the R&D division.
As devices grow in complexity, high-quality software becomes more critical to performance, and development time increases. This can lead to the potential of software not meeting internal qualifying standards and contributing to delivery delays.
In response to these issues, New Software Process Review initiatives ("nSPR initiatives") were adopted in 2008 with the cooperation of the R&D division. Under these initiatives, the quality assurance division participates in the development planning and design reviews for certain products from the upstream processes of development, to confirm the deliverables (specifications) at each stage of development and provide prompt feedback on problems in order to improve the quality of development deliverables.
During nSPR initiatives conducted during fiscal 2011, the quality assurance division regularly confirmed whether there were omissions in development plan work items during the planning phase and whether there were any issues or risks relating to plan progress. Furthermore, in response to development deliverables (specifications), the quality assurance division confirmed whether there were omissions in the contents of specifications for each step of the development process and provided feedback to the R&D division on potential issues. In addition, after development completion, the quality assurance division identified areas needing improvement to ensure the same problems would not be repeated in future software development.
As a result, when software (A) for test systems manufactured before the adoption of nSPR initiatives is compared with software developed (B) for test systems after the adoption of nSPR initiatives, it is apparent that the number of defects after software shipment was reduced by approximately 1/5 for (B) compared to (A). In addition, the period of time required by the quality assurance division to confirm quality was reduced by approximately 1/8 for (B) compared to (A), allowing us to provide high-quality products to customers in a timely manner.
From fiscal 2012, in order to implement nSPR initiatives for all software products, we will revise our product certification system for software as we aim for even further quality improvement and more timely delivery.
Benefits of new software process review activities
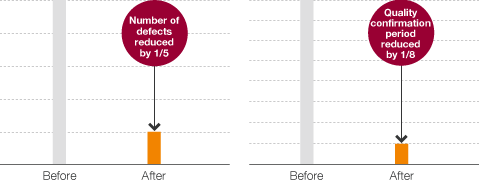